The “Optical, Mechanical and Electrotechnical Institute” founded in 1900 under the leadership of Ernst Buchner has blossomed into one of the global leaders offering powerful solutions for human-machine communication: With a workforce of over 2000, subsidiaries around the globe and manufacturing plants in Europe, the US and China, the RAFI group is among the top leaders in the industry. And the company expects the same top performance and innovative capabilities from its partners and suppliers. In one of its specialities – the soldering process – RAFI relies on SEHO’s technology and competence.
At RAFI’s headquarters in Berg/Ravensburg, traditional German pragmatism and reliability meet international innovation. The company has set itself a high bar: RAFI products make things happen at the push of a button.
RAFI has been committed to progress right from the start. The company’s pioneering spirit and innovative strength and the exceptional know-how of its workforce have enabled it time and again to introduce trail-blazing new products to the market and to win first place in innovation competitions.
Quality and reliability are the main criteria for the product portfolio, which includes components, HMI systems and EMS. All of RAFI’s employees share in the philosophy that every good thing can still be made a little bit better. With its focus on exceptional and tangible product quality, the company will only consider ultra-modern plant engineering solutions that support highly flexible manufacturing workflows.
“Our procurement of new manufacturing equipment is defined by a range of factors,” explains Romano Reising, process technology expert at RAFI’s Electronics division. “In addition to a solid partnership with our suppliers, we primarily look for innovation and new ideas that help us further optimize our manufacturing processes so that ultimately, we can offer better quality and more flexibility to our customers.”
It is precisely these innovative ideas that are embodied in SEHO’s MWS 2340 wave soldering system that was recently installed at RAFI’s factory in Berg. “This, too, demonstrates RAFI’s pioneering spirit,” says Romano Reising with a smile, “the latest features of this system were used in our production process even before the product was officially launched on the market.”
The modular concept of the MWS 2340 provides maximum flexibility. The system stands out in particular for its extremely high degree of automation and many innovative features for monitoring and controlling soldering processes.
The fluxing area is equipped with a spray fluxer with HVLP technology (high volume – low pressure) that ensures a homogeneous spray pattern when the flux is applied. The assembly dimensions are customizable, which means that there is less environmental impact and at the same time, a sustainable cost reduction can be achieved by lowering the consumption of flux. In order to meet RAFI’s high quality requirements, an additional flux volume monitoring feature was integrated that detects the relevant flow rate while flux is being applied. If an error is detected, the monitor outputs a corresponding message and records all values in the operating data log. “The proper application of flux is crucial for the quality of a solder joint,” explains Romano Reising. “This volume monitor provides detailed evidential data for the parameters of a manufactured assembly even years later.”
RAFI will use the new production line in 3-shift operation for the manufacturing of a broad range of products with highly diverse assemblies for medical engineering, the automotive industry and telecommunications. Individual products may weigh up to 10 kg including their soldering frames, which accordingly creates high heat requirements. This demands high flexibility of the system technology.
Despite its compact size, the new MWS 2340 at the RAFI factory includes a pre-heating section of 3300 mm. The customizable pre-heating area consists of a convection pre-heating zone that provides for an even warm-up of the assemblies. The required flexibility is provided by the eight pulsar pre-heating zones that follow. The new pulsar emitters combine the benefits of conventional quartz and infrared radiators and stand out for their high energy density. A particular benefit is their especially high efficiency which is achieved through the extremely fast reaction speed of the pulsar emitters in combination with an exact monitoring system and the individual actuation of the heating elements. This pre-heating concept is based on the activation of individual emitters rather than entire pre-heating segments. This makes it possible to apply the specific, exact amount of thermal energy to each product that is needed for the process without losing out on cycle time. As a result, high-mix manufacturing – even of assemblies with different thermal requirements – and high-volume production are no longer impossible to combine. This is the kind of flexibility that RAFI really appreciates. “Our older systems used a transport speed of 120 cm/min. during production and still, for some assemblies it was a challenge to introduce enough heat into the product,” says Romano Reising. “With the new pre-heating concept, we use a speed of 140 cm/min., and we have not yet reached the limit. There is still more room to manoeuvre, for example for high-performance electronics.”
The electronics manufacturing at RAFI requires the use of solder masks depending on the specific product. The mask cut-outs vary in size from 5 mm to 10 mm. “Sometimes it was a bit tricky to achieve really good solder joints,” says Romano Reising.
The new system’s soldering area is fitted with two solder nozzles that create turbulent waves, which make them suitable for a wide variety of different products.
The automatic nozzle height adjustment is a particular highlight. This new MWS 2340 feature allows for the software-controlled height adjustment of the individual solder nozzles over a distance of 20 mm; this allows setting the optimal distance between the circuit board and the solder nozzle for each product. This means independence from the workpiece carrier design without any impact on the cycle time.
“The automatic nozzle height adjustment provides additional process stability and higher product quality because all solder joints are reliably wetted and a defined solder peel-off can be achieved,” explains Alexander Riedel, Key Account Manager at SEHO and point of contact for the RAFI Group. Romano Reising adds: “Currently, our solder programs for the different products are designed in such a way that the pulsar emitters are programmed individually depending on the thermal requirement of the respective assemblies. The nozzle height is adjusted between 3 mm and 4 mm and is absolutely reproducible, even after servicing. Like the pre-heating power, there are still plenty of reserves for the nozzle height adjustment, so we are optimally prepared for new applications. On the whole, we can say that the combination of pulsar emitters and the new nozzle height adjustment is simply the best system there is.”
With a view to product quality as the top priority, the new MWS system at RAFI was expanded with other features that mainly pursue one goal: increase process stability even further.
This also includes the stability of the nitrogen atmosphere inside the system. Nitrogen provides multiple benefits to the wave soldering process, primarily the higher wetting activity which ultimately decides the quality of the solder joints.
The active extraction controller at the intake and exit of the system ensures the stability of the nitrogen atmosphere. Unsymmetric airflows in the tunnel are compensated, and the system responds automatically to changing external factors.
“Solder balls continue to be a frequent phenomenon in the manufacturing of electronic assemblies,” says Alexander Riedel. Solder balls can detach later when the assembly is in use, and can cause short-circuits. For this issue in particular, defect prevention must come before defect elimination. Depending on the application, if the nitrogen atmosphere during the soldering process is too good, this can promote the formation of solder balls. “Our experience has shown that a value of 350 – 400 ppm of residual oxygen yields the best results,” explains Romano Reising. In order to guarantee this target value consistently, a controlled aeration management function was added to the system. The residual oxygen is measured constantly and if needed, raised to the desired level.
“Another function is now available for the MWS 2340 that also aims at increasing process stability for wave soldering,” says Alexander Riedel. A crucial factor for process stability is of course the stability of the solder wave height. But up until now, it was not possible to measure the wave height without disrupting the production process and applying external test instruments, and there was no automatic adjustment.
In view of these issues, SEHO developed an automatic wave height measuring feature that guarantees stable processes across the entire soldering width both for laminar and turbulent waves. Inside a configurable tolerance range, the system automatically regulates the wave height to the correct value based on the measured values and a mathematical model. “By the way, the automatic wave height measurement feature can be retrofitted in newer systems,” says Alexander Riedel with a smile and a sideways glance at Romano Reising.
“For some of the new features, such as the automatic nozzle height adjustment, we were able to play an active role during the development stage and were constantly sharing information with the product management at SEHO,” says Romano Reising. Regarding the collaboration with SEHO, RAFI did not just value the high quality standards of the machines and the advanced technology but also the competence and reliability of their contacts. “Sometimes there are technical challenges that need to be solved – that is unavoidable,” says Romano Reising. “How a company handles such situations, that really tells you how good they are.”
This shows how collaboration among partners can turn initial ideas into technology solutions.
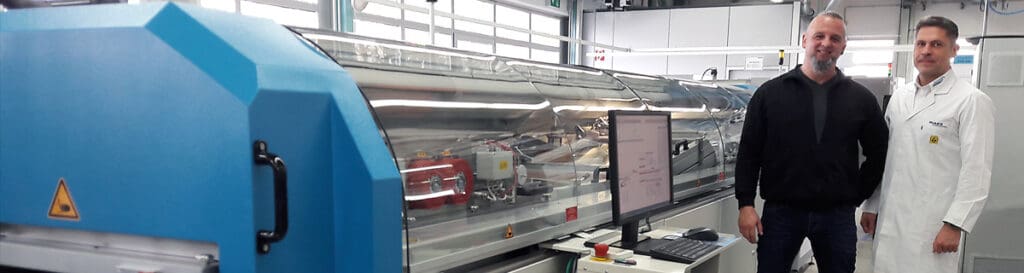